BBillyC
Well-Known Member
Well I finally got up enough guts to do this. I narrowed 3-1/2" per side. I squared up everything on the from the front torsion bar frame which worked great. I made my own hangers and only wanted the hole. I used 12" 3.5" x 3.5" and marked it out on the frame. You can see a little notch at the front. Tomorrow I will set up the shackle perches. I measured the stock spring width at the original hanger and at the shackle perches and they are both 44" on center, so they are parallel. I dumped the photos on photo bucket so we'll see how this works posting them.
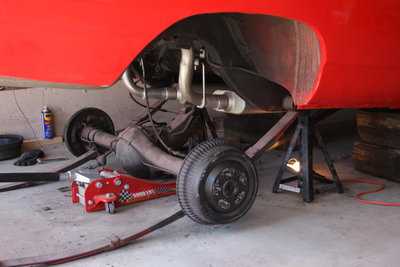
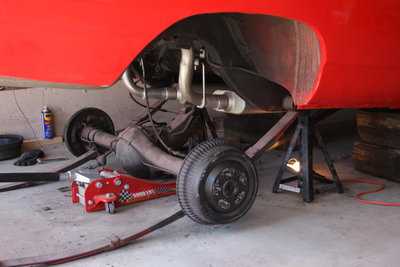